Electrochemical
Cleaning, Polishing, Marking
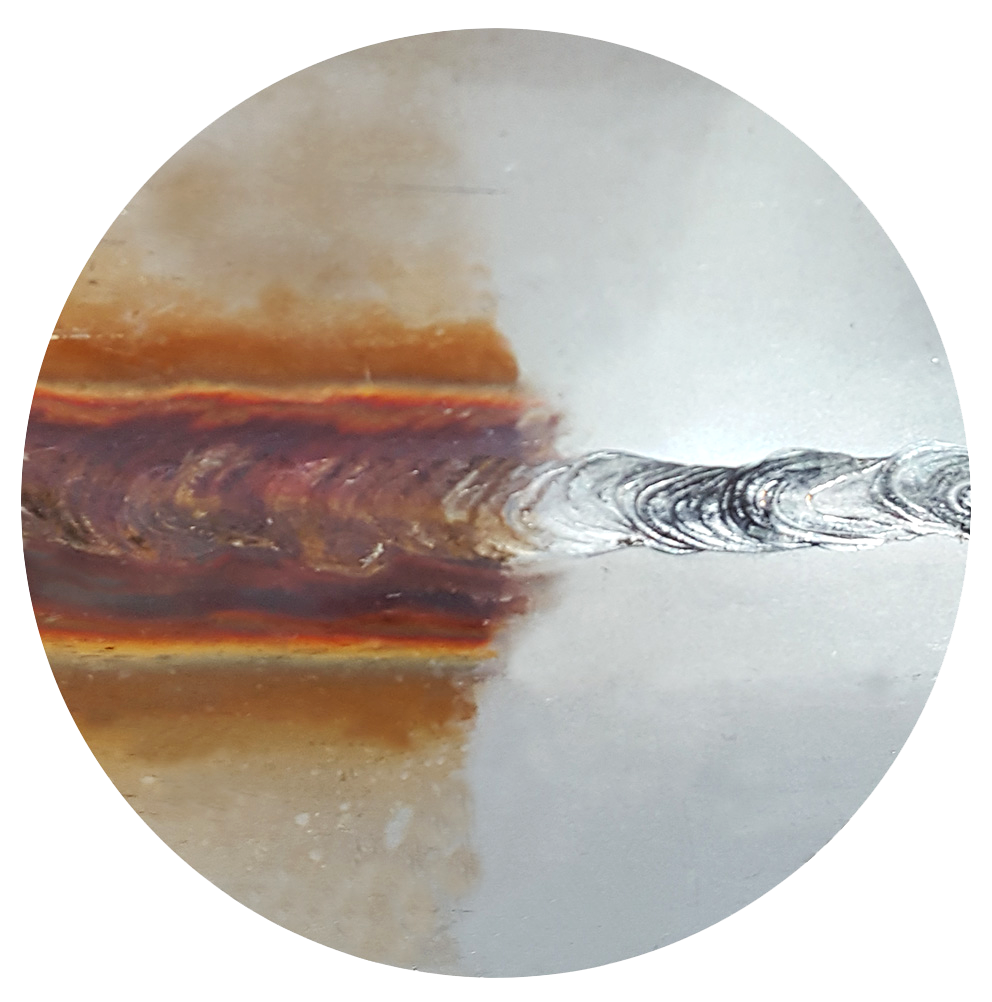
Welding seam
before / after cleaning
The process
Take a million carbon fibres, a good 100 A continuous current, plus the right electrolyte: the welder has never polished so quickly. This solves the main welding dilemma – tarnish, scaling and rust, which are caused by the destruction of the passive layer during welding, are simply brushed away.
Magic? No – electrochemistry!
This is made possible by the high energy density and the conductivity of the up to 4.5 million carbon fibres: electric arcs are created at the tip of the fibres. These remove tarnish, oxidation and even light scaling in a flash, without damaging the surface.
Our cleaning electrolyte is the non-toxic food additive E338, also known from cola drinks. It cools, increases the electrical conductivity and protects against renewed overheating by evaporation. The oxygen split off in the process combines on the metal surface to form chromium oxide: in this way, the protective passive layer is restored in the same operation. This effect has been certified by the Federal Institute for Materials Research.
The cleaning effect is therefore not created by etching or grinding, but is gentle on the surface due to the extremely high energy density. When brushing, the carbon fibres nestle exactly to the shape of the workpiece; by flexibly extending the fibres from the Teflon sleeve, corners and crevices can also be reached. Suitable brush shapes and sizes are available for every cleaning task.
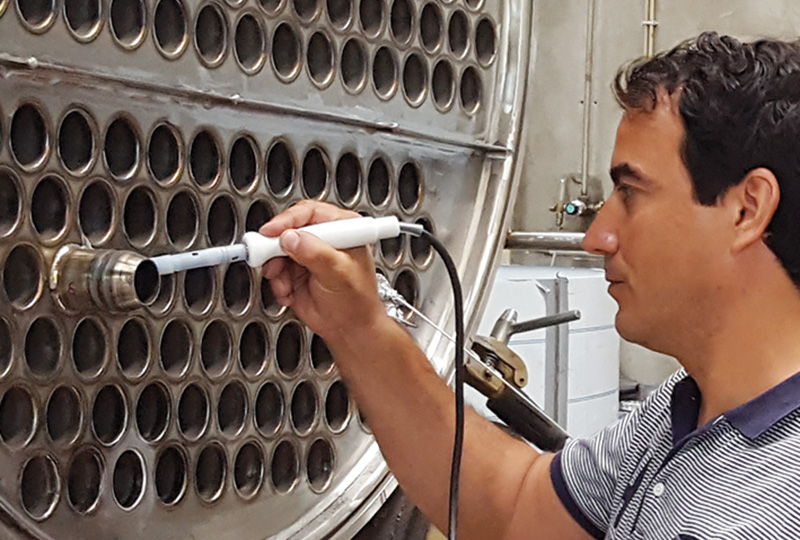
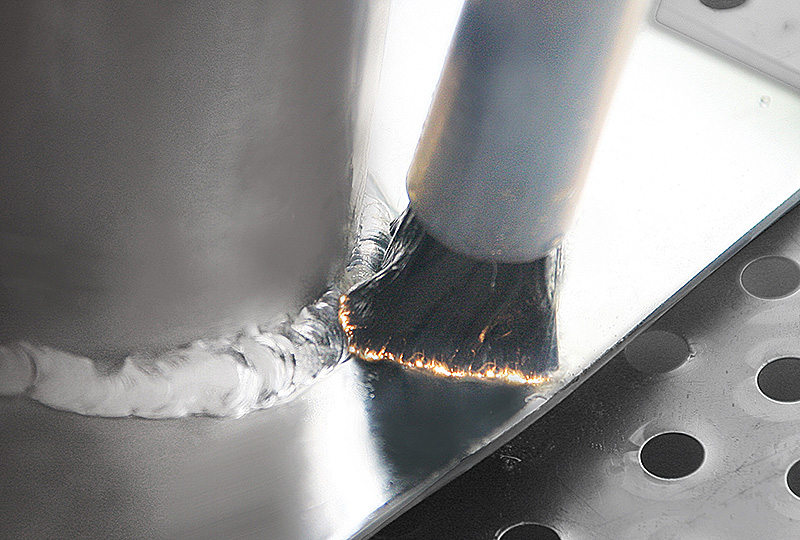
Millions of small electrical charges
remove tarnish colors, oxidation layers and even
minor scaling
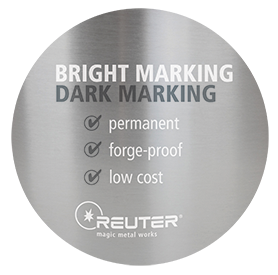
Mirror-smooth polish
Our switchable AC/DC devices also facilitate direct current (DC) mode for high-gloss polishing. Strong discolouration can be removed or evened out and dull areas in the heat-impact zone can be treated to the desired level of gloss.
Forgery-proof marking
A writing template or label printer can be used to produce individual signatures on your work pieces. Dark marking applies an oxidation layer to the surface; bright marking removes parts of the surface – like engraving, but does not look dark. Both methods are permanent and resistant against chemicals and abrasion – and are therefore often used for surgical instruments, tools, sanitary fittings, etc.